Customer Spotlight: Meet the Laser Cladding “It Guys” at American Cladding Technologies
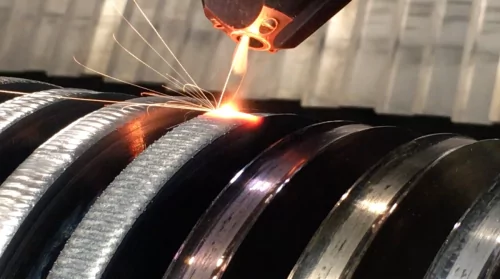
Self-described as the American Cladiators, the team at American Cladding Technologies (ACT) are the “it guys” for getting tough jobs done. ACT specializes in laser cladding technologies and additive manufacturing to strengthen, restore and improve surfaces of metal parts. These parts such as valve balls, hard facing screws, nozzles, plates or drill bits are used in an array of industries ranging from nuclear power generation, aerospace, public infrastructure, and oil and gas exploration. ACT most typically uses tungsten carbide, stainless steel, titanium carbide, Inconel 625 and aluminum silicon magnesium alloys in their deposition process.
So what exactly is laser cladding? The process of laser cladding works by adding metal alloy powder layer upon layer as a bond onto a base material or substrate. “Powdered alloy is delivered through a powder feed system (vibratory or rotary disk) using a carrier gas such as argon or helium. The powder is delivered through a non-static plastic tube to the nozzle head. The powder is delivered to the melt pool either coaxial or through discrete streams depending on the nozzle type used. Off-axis powder delivery is commonly used as well” explains Chris Proulx, ACT’s Vice President of Sales and Marketing.
The process protects the integrity of the original substrate and is a very low heat process with a low heat affect zone, resulting in little to no distortion. Their services are designed to improve the metal part by adding protective layers for erosion, corrosion or further wear. ACT is also capable of repairing parts that are damaged by rust, dents, dings or holes by machining the piece to clean and prep for proper cladding. Their technology can clad a piece up to 40’ in length, 6’ in diameter, and up to 6 tons in weight. ACT’s laser cladding process has been known to extend the life of their customer’s parts well beyond the initial life expectancy.
“We take a lot of pride in our R&D” says Proulx. Their new 20,000 ft2 facility in East Granby, CT can annually process up to 32 tons of powder deposition. Though many of their projects are focused on repair, ACT welcomes OEM projects especially with the recent acquisition of their Trumpf TruPrint 3000 metal 3D printer, which will enable them to design and print parts that were not possible with their earlier machining capabilities.
They are known as the “go to guys” when it comes to laser cladding in the world of high strength wear protection. When companies struggle to coat in house or fix the wear issue of their parts self-sufficiently, they turn to ACT. “We give another layer of options to our customers”, says Jeff Whittaker ACT’s President about their product and surface hardening solutions.
In the world of additive manufacturing, aluminum powders are vital. Their desirable characteristics of fine microstructures, high heat conductivity and low weight make for ideal performance characteristics when compared to other alloys. Recently, ACT purchased aluminum magnesium silicon powder from READE for a space exploration project that required powders best suited for highly corrosive environments where weight is a limiting factor. Their customer needed a free form aluminum tube and their bespoke manufacturing capabilities were called upon. “READE was great to work with, very responsive and helpful in identifying different aluminum alloys” says Whittaker.
Working closely with custom manufacturers is one of the many highlights of managing accounts at READE. The spirit of a can-do attitude runs deep at ACT. Their custom process is designed to meet the needs of their customers while adding the desired performance characteristics (wear protection) to the parts they are working on (tasked with improving). Likewise, READE, offers customized powder solutions to customers while focusing on quality and meeting customer demands in today’s fast paced industrial marketplace.
READE looks forward to a mutually rewarding relationship with ACT as they embrace their new 3D printing capabilities and expand their products and services to an ever-changing customer base.
ABOUT READE
As a Women Led Service-Disabled Veteran-Owned Small Business, READE supplies specialty chemical solids for nearly every industry. READE combines their roots in chemistry dating back to 1873 with supply chain expertise and customer service innovation to enable our customers to meet the needs of their manufacturing demands. With an extensive inorganic product line, READE represents over 2,000 manufacturers as a global distributor, value-added toll processor and packager
CONTACT
Director of Marketing
Elisabeth Law, +1-401-433-7000
Elaw@reade.com